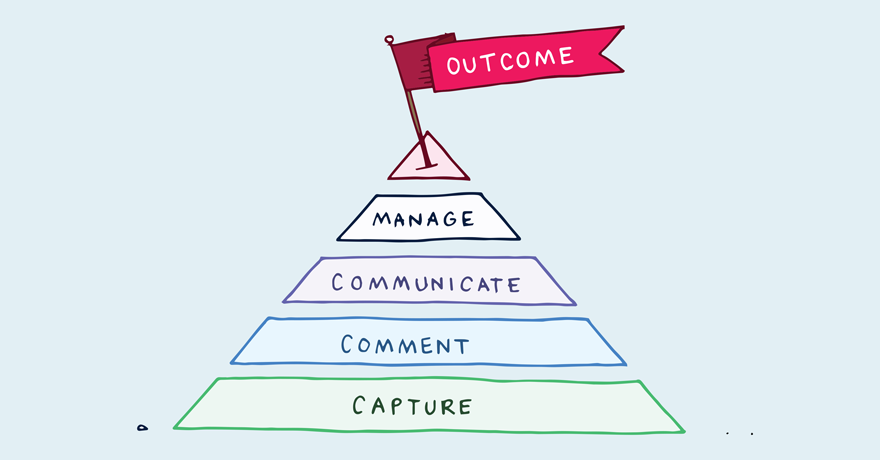
The problem of jumbled conversations
Imagine you’re in a meeting to plan a new building. There would be discussion about consents, foundations, land, structure, cladding among other things. Now, imagine that the discussion is a jumble of different ideas all being chipped in randomly. One minute you’re discussing the grade of steel to be used. The next someone says they’ve seen a nice new couch that could go in the foyer. From nowhere someone adds a deep and meaningful comment about how the building should lift and empower people. Now imagine that despite all the energetic talking, a suitable roof isn’t included in the project! It’s an unlikely example. That’s because in general, people are familiar with the design and build process used in construction.
But when the topic is using data and metrics to improve manufacturing, there isn’t any agreed structure or commonly known process. The art and science of doing this well is still in its infancy. Because of this I’ve found that many of my initial conversations with people are all over the place.
Enter the pyramid diagram
The pyramid diagram is a simple tool to make life less confusing. In the rest of this post, I’ll explain what it is, why it’s shaped like a pyramid and how you can use it.
The pyramid
The pyramid has four process layers underneath the pinnacle, which is the goals that we set for ourselves.
- The base process is Capture. Capture is the collection of raw data from what the process is doing. This would be production starts and stops, running speed, modes, temperatures etc.
- The next process is Comment. Commenting is adding the human element. This element tends to be the ‘why’ part. Why did a process stop? Why did it overheat?
- Above this is Communicate. Good communication often involves summaries, analysis and visuals. It asks who is the user of this information and what will they do with it?
- Next is the Manage layer. Management needs to create the right environment for decisions to be made and action to be taken. Don’t misread this; it doesn’t mean that management needs to take all the action!
- At the top, there is the Desired Outcome. The specifics of this will vary from business to business. But it’s a safe bet that most manufacturers want sustained, evidenced improvement.
Why a pyramid shape?
So why are the layers put into a pyramid shape? I find that the pyramid is helpful in seeing how the layers relate. For example, without a solid base of facts, you can’t manage properly. In more detail, captured raw data lets commenting take place. Then we can communicate very efficiently. With all this in place management can put in place the right environment for change, which then leads to the desired outcome.
How to use it
Try doing the following:
- Draw and label the pyramid. Brainstorm out words, ideas, plans or components that you have in place or in mind. Place them onto the pyramid.
- Look for any weaknesses or holes on the pyramid. A missing or weak layer will hamper progress towards the outcome.
- Look for double ups and excessive effort. The pyramid can reveal that more than one person or team might be trying to crack the same nut.
- Create a to do list to deal with the gaps and double ups that you found.
- Note down a date to review your diagram, to check on progress and amend any plans. A good question to ask during the review is “is there evidence that we are making progress to the desired outcome.” If not, why not?
Final thoughts
I spend a lot of time with manufacturing managers. What I’ve noticed is that they often have some activity capturing and communicating data. That is, they collect numbers and put them on graphs. However, the commenting and management layers need more work. I referenced a New Zealand research paper in our last newsletter. You can find it here. I think it says a similar thing.
How DataNow can help
DataNow is a platform specifically designed to help you capture, comment and communicate manufacturing facts throughout your business. It takes care of much of the heavy lifting in the lower layers of the pyramid. If you’re motivated to become a more data driven manager, contact us today and ask how we may be able to help you on your journey to manufacturing success.